制造业5大搬物流机器人:
1. 多关节机械臂机器人
- 核心特点:六轴自由度设计,灵活性高,可完成搬运、焊接、码垛等复杂任务。
- 典型应用:汽车生产线(车身焊接、部件装配)、精密仪器搬运。
- 代表型号:库卡KR系列、发那科M-2000iA(载重达1.2吨)。
2. AGV/AMR自主移动机器人
- 核心特点:激光SLAM/VSLAM导航,动态路径规划,支持跨楼层作业。
- 典型应用:
- 潜伏式AMR:电子厂线边物料转运(如迈睿潜伏系列,负载400–2000kg);
- 叉取式AGV:仓储托盘搬运(如中力搬马机器人,支持电梯联动)。
- 效率提升:京东物流案例中,AMR集群调度提升拣选效率3倍。
3. SCARA平面关节机器人
- 核心特点:四轴结构,成本低、速度快,平面定位精度±0.02mm。
- 典型应用:3C电子装配(电路板搬运)、食品包装线(高速分拣)。
- 优势:成本仅为六轴机器人的一半,适合轻量化高频任务。
4. 智能搬运机器人系统
- 核心技术:AI视觉识别+多传感器融合(如力控、3D视觉),自适应复杂环境。
- 场景案例:
- 汽车厂:硬臂式助力机器人搬运重型工件(如车身底盘);
- 医药仓储:料箱机器人(迈睿T6)实现多箱协同转运。
- 安全性:动态避障响应时间<0.1秒,人机混场作业0事故。
5. 协作式搬运机器人
- 核心特点:力控感知+人机协同,无防护栏作业,编程简易。
- 典型场景:
- 医疗器械:手术器械无菌搬运(防尘设计);
- 柔性产线:与工人协同装配小型零件(如T型助力机器人)。
- 创新设计:模块化夹具,5分钟内切换抓取对象。
精准选型适配场景——成本节省30%+
按载重与精度需求分层部署
重型搬运(>500kg):选用移动复合机器人(如汽车焊装车间案例),载重1吨,重复定位精度±0.05mm,替代人工搬运焊接件,单台年省人力成本48万元;
轻型高频搬运:AMR机器人(载重500kg),跨楼层配送,日均搬运300-500趟,效率=3名工人,单台年省18万元。
精密搬运(±0.2mm):六维力控机器人(如电子行业),防静电夹具抓取芯片,次品率从4%降至1%,单线年省240万元。
场景化技术匹配
汽车厂:移动复合机器人+激光SLAM导航,适应动态焊装环境;
智能仓库:AMR集群调度系统,跨楼层无缝衔接原料→成品库;
无尘车间:防尘AMR+无菌夹具,满足医疗/食品行业标准。
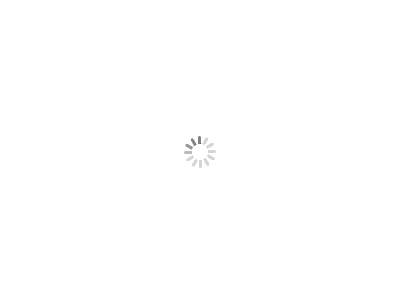
分阶段投资+政策套利——缩短回本周期50%
试点验证→规模化扩展
试点阶段:单产线投入2台AMR(成本约60万),3个月验证效率提升40%→申请政府补贴;
规模扩展:利用补贴(设备采购额20%-30%)降低总投入,如某车企获补300万,总成本从1200万降至900万。
政策红利最大化
补贴类型:智能制造设备补贴(上海30%)、技改专项资金(深圳20%);
申报技巧:绑定“机器换人”政策关键词,突出减员增效数据(如人力节省50%+)。
人机协同重构岗位——增效降本双突破
-
人力结构优化模型
岗位类型 |
优化方案 |
成本效益 |
低技能搬运工 |
AMR完全替代(10台替代40人) |
年省480万,维护成本仅5% |
高技能操作员 |
转岗为机器人运维师 |
培训成本50万,故障响应提速60% |
生产调度员 |
人机协同系统管理 |
KPI达标率提升至95% |
-
培训体系搭建
- 课程设计:机器人编程(40课时)+故障诊断(30课时),考核通过率>90%;
- 激励机制:“最佳人机搭档”评选,奖金+荣誉双驱动。
- 维护成本压缩技巧
- 预测性维护:物联网传感器监测电机温度/振动,故障率↓40%;
- 模块化更换:机械臂关节等部件快速替换,停产时间<2小时。
风险对冲与柔性部署——保障收益稳定性
-
技术风险管控
- 双供应商策略:核心部件(如激光雷达)采购自2家厂商,断供风险↓80%;
- 协议兼容性验证:提前测试与MES/PLC系统的接口,调试周期缩短50%。
-
运营风险对冲
- 阶梯式外包:非核心运维分阶段外包,首年外包比例30%,次年降至10%;
- 保险覆盖:购买机器人停工险,弥补意外停产损失。